Expert Tips on Implementing Foam Control in Chemical Processing Environments
Expert Tips on Implementing Foam Control in Chemical Processing Environments
Blog Article
The Role of Foam Control in Enhancing Item Top Quality and Performance
Foam control is an often-overlooked yet important component in the search of item high quality and operational performance throughout diverse industries. This discussion will certainly check out the multifaceted impact of foam on both item honesty and manufacturing processes, raising important inquiries about the strategies that can be used to optimize foam control.
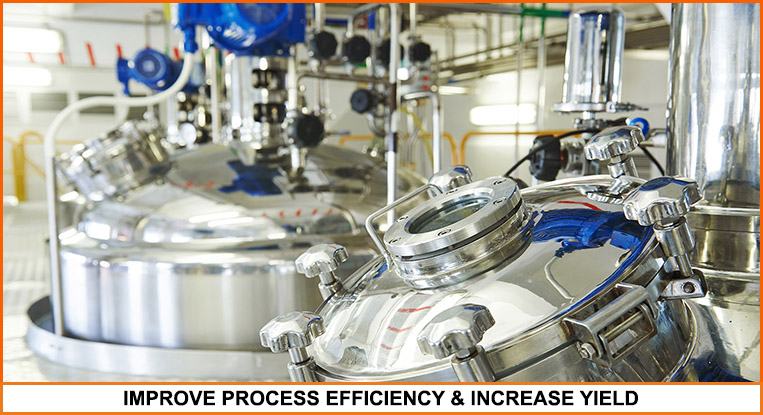
Understanding Foam Formation
Foam formation is a complex phenomenon that can significantly impact item top quality and functional performance throughout numerous sectors. It takes place when gas bubbles come to be trapped in a fluid, leading to the creation of a frothy framework. Several factors contribute to this procedure, including the chemical and physical buildings of the liquid, the presence of surfactants, and the conditions under which mixing occurs. Understanding these variables is crucial for handling foam properly.
The fluid's thickness and surface stress play crucial roles in foam stability. Surfactants, as an example, can minimize surface tension, advertising bubble development yet likewise enhancing foam stability, which can be problematic in particular applications. Mechanical anxiety, temperature level changes, and the visibility of contaminations can intensify foam generation, making it crucial to monitor these aspects throughout manufacturing procedures.
Industries such as food and drink, drugs, and chemical production must be particularly alert pertaining to foam control. By realizing the hidden devices of foam development, companies can apply targeted strategies to reduce its impacts, thus protecting functional effectiveness and making certain regular product performance.
Effect On Product Quality
The visibility of foam can considerably jeopardize item quality throughout various markets. In manufacturing processes such as food and beverage, drugs, and cosmetics, excessive foam can cause irregular product solutions. For instance, in food production, foam might catch air, influencing texture and flavor, which can eventually modify customer perception and complete satisfaction.
Furthermore, foam can impede the harmony of paints and finishes, leading to flaws like bubbles and unequal surfaces. In pharmaceutical applications, foam can interfere with the precise dosing of fluid medicines, possibly affecting therapeutic efficacy and individual security. These top quality problems not only diminish the end product's appeal but can likewise cause expensive recalls and damages to brand track record.
Furthermore, the visibility of foam can make complex quality control actions, making it difficult to attain regular results and precise measurements. Efficient foam control not only mitigates these dangers but likewise boosts total product high quality by guaranteeing that formulas meet strict sector standards. By spending in foam control strategies, business can secure their items, enhance customer complete satisfaction, and keep a competitive edge in the industry.
Operational Difficulties From Foam
Reliable operations in different sectors can be badly disrupted by the existence of foam, which postures multiple difficulties throughout manufacturing processes. Foam can impede mixing and response times, hampering the effectiveness of chemical processes. In sectors such as food and beverage, foam formation can result in inaccurate fill degrees, resulting in item waste and variances in packaging.

In atmospheres where hygiene is vital, such as drugs and food handling, foam can complicate cleansing procedures, developing covert reservoirs for contaminants. This not just increases top quality worries yet likewise can bring about compliance concerns with regulative requirements.
Furthermore, the psychological influence on operators can not be neglected; extreme foam can create a disorderly job setting, bring about decreased morale and productivity. In summary, resolving the functional difficulties posed by foam is important to keeping effectiveness and product quality in various markets.
Techniques for Reliable Foam Control
Exactly how can industries successfully alleviate the difficulties posed by foam? Reliable foam control approaches are vital for enhancing product high quality and functional efficiency.
Along with chemical options, process optimization plays a critical function in foam monitoring. Industries can examine and adjust specifications such as blending pressure, temperature, and rate to reduce foam generation. Implementing devices modifications, like setting up foam-breaking tools or adjusting tank layout, can further help decrease foam levels.
Normal tracking and evaluation of foam behavior within production procedures are additionally crucial. Utilizing innovative sensing units and analytics can provide real-time information, permitting for timely treatments and adjustments. Personnel training is just as important; click here for more info ensuring that personnel are well-informed regarding foam characteristics and control strategies can result in proactive foam administration.
Instance Researches and Industry Applications
While lots of markets face unique difficulties connected to foam control, case researches expose that tailored approaches can significantly enhance both item top quality and functional efficiency. In the pharmaceutical sector, for circumstances, a leading maker executed a custom foam control approach that lowered foam formation during fermentation procedures. This advancement not only improved return by 15% yet likewise reduced contamination risks, ensuring greater product honesty.
Likewise, in the food and over at this website beverage sector, a significant dairy products producer confronted too much foam throughout pasteurization - Foam Control. By presenting a specialized antifoam agent, they reduced processing time by 20%, which directly translated to raised throughput and lowered energy intake. The application of foam control measures ensured consistent product appearance and taste, strengthening brand commitment
In the chemical production market, a case study highlighted the successful application of foam control in wastewater treatment procedures. The application of a real-time tracking system enabled operators to change antifoam dose dynamically, leading to a 30% reduction in chemical usage and improved effluent quality.
These case studies highlight the diverse applications of foam control throughout markets, highlighting its important role in boosting item top quality and operational efficiency.
Final Thought
In final thought, efficient foam control is indispensable to enhancing product top quality and operational performance throughout various sectors. By resolving foam formation, organizations can alleviate the unfavorable impacts on formulations, structure, and dosing precision. Implementing targeted foam monitoring approaches not from this source only lowers processing delays and waste but additionally boosts tools dependability. Ultimately, prioritizing foam control contributes to enhanced efficiency, safeguarding brand online reputation, and raising consumer complete satisfaction, highlighting its importance in quality control within manufacturing processes.
Foam control is an often-overlooked yet important component in the pursuit of item high quality and operational efficiency throughout varied markets. Staff training is equally important; ensuring that employees are educated regarding foam dynamics and control techniques can lead to positive foam administration.
While many industries encounter special challenges related to foam control, instance research studies expose that tailored approaches can dramatically improve both product top quality and functional effectiveness (Foam Control). In the pharmaceutical industry, for circumstances, a leading maker executed a custom foam control approach that decreased foam formation throughout fermentation procedures.In conclusion, reliable foam control is indispensable to boosting item quality and functional efficiency throughout different markets
Report this page